Double Crank Press (110-250 Tons), APC Series
Double Crank Power Press | Metal Forming Processes | 110 - 250 Metric Tons Capacity
APC series double crank presses are outstanding pieces of metalworking machine tools that are designed for precise station stamping processes. The wide multi-point slider guide design of the crank press effectively minimizes vibration during operation and maximizes precision stamping. There are four models of the double crank press. We produce 4 models of these mechanical presses with stamping capacity of 110tons, 160tons, 200tons and 250tons.
Super Rigid Steel Frame
With a highly rigid frame constructed from high-quality steel plate, the stamping press for automotive parts benefits from incredible stability and strength that leads to precise and reliable operation. The machine’s alloy steel structure features an optimized double wide working area for large scale stamping operations.
Stable performance
In order to maintain stability during stamping operation, the metal forming press is equipped with two balancers and a highly sensitive clutch/brake system.
Highly Responsive Hydraulic Overload Protector (HOLP)
The double crank press's HOLP system relieves the pressure that builds up during a tonnage overload in milliseconds and protects both the press and the work piece. If an overload occurs, even on just one side of the press, the oil pressure in the cylinder is quickly released by the magnetic safety valve and the machine will shut down. The oil dump feature and unique dual-valve pressure switch arrangement is highly reliable and can be reset quickly and easily by inching the slide back to center, which automatically reactivates the pump and builds up the hydraulic pressure to a safe level.
1.Dry clutch brake
2.Standard operating system
3.Model choice/switching/adjusting/one stroke/continuous operating
4.Oil pressure overload protection device
5.Over-run safety device
6.Magnetic safety valve
7.Misfeed detection device
8.Electric slide adjusting device
9.Digital die height indicator (unit: 0.1 mm)
10.Electric lubricating device
11.Accumulative counter (6 digits)
12.Preset counter (6 digits)
13.Maintenance counter (6 digits)
14.Life counter (6 digits)
15.Electronic rotary cam switch (6 connections)
16.Air jetting device 1/2"primary circuit
17.Air source connector 1/2“ secondary circuit
18.Error detection socket
19.Power socket (only apply to single-phase 110V power)
1.Wet clutch brake
2.Die cushion device
3.Vs variable-speed motor
4.Touch-screen device
5.Photo-electric safety device
6.Upper slide feeding device
7.Main motor inversion device
8.Foot switch
9.Safety stop and safety plug
10.T-type double handed button operating floor
11.Inspection variable connection magnetic valve
12.Anti-vibration mechanical foot
13.Rapid mold exchanging device
14.Upper die clamper
15.Lower die clamper
16.Die lifter
17.Mold-shift arm
18.Basic bolt and soleplate
19.Automatic feeding device
20.Three-in-one NC straightening feeder
21.NC idler wheel feeder
22.Two-in-one feeder and straightening machine
23.Straightening machine
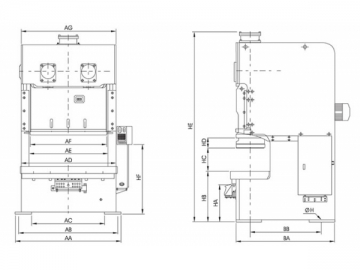
Model | APC-110 | APC-160 | APC-200 | APC-250 | ||||
V | H | V | H | V | H | V | H | |
AA | 2000 | 2200 | 2620 | 3000 | ||||
AB | 1900 | 2080 | 2460 | 2800 | ||||
AC | 1360 | 1520 | 1820 | 2200 | ||||
AD | 1800 | 2000 | 2400 | 2700 | ||||
AE | 1510 | 1660 | 1990 | 2220 | ||||
AF | 1400 | 1600 | 1850 | 2100 | ||||
AG | 1780 | 1980 | 2320 | 2590 | ||||
BA | 1745 | 1940 | 2235 | 2545 | ||||
BB | 1295 | 1380 | 1885 | 2195 | ||||
BC | 650 | 760 | 840 | 900 | ||||
BD | 330 | 385 | 425 | 455 | ||||
BE | 500 | 550 | 650 | 700 | ||||
HA | (630) | (730) | (790) | (820) | ||||
HB | 830 | 865 | 990 | 1025 | 1070 | 1120 | 1100 | 1155 |
HC | 400 | 435 | 450 | 485 | 500 | 550 | 550 | 605 |
HD | 180 | 110 | 200 | 130 | 250 | 150 | 280 | 170 |
HE | 3059 | 3709 | 3849 | 4304 | ||||
HF | 1240 | 1440 | 1570 | 1680 | ||||
0h | 035 | 047 | 054 | 054 |
Name | Unit | APC-110 | APC-160 | APC-200 | APC-250 | ||||
Model | V | H | V | H | V | H | V | H | |
Capacity | Ton | 110 | 160 | 200 | 250 | ||||
Rated tonnage point | mm | 5 | 3 | 6 | 3 | 6 | 3 | 7 | 3.5 |
Stroke | mm | 180 | 110 | 200 | 130 | 250 | 150 | 280 | 170 |
Variable speed | s.p.m | 35-65 | 50-100 | 30-55 | 40-85 | 25-45 | 35-70 | 20-35 | 30-60 |
Die height | mm | 400 | 435 | 450 | 485 | 500 | 550 | 550 | 605 |
Slide adjustment | mm | 100 | 100 | 120 | 120 | ||||
Bolster area | mm | 1800×650×130 | 2000×760×150 | 2400×840×170 | 2700×900×170 | ||||
Slide area | mm | 1400×500×70 | 1600×550×70 | 1850×650×95 | 2100×700×95 | ||||
Main motor | kw×P | 11×4 | 15×4 | 18.5×4 | 22×4 | ||||
Press weight | Ton | 14.2 | 20 | 27.5 | 45.5 | ||||
Air pressure | kg/cm2 | 5 | 5 | 5 | 5 | ||||
Press precision | JIS(CNS) 1 class | ||||||||
Die cushion capacity | Two plate & two cylinders | ||||||||
Capacity | Ton | 3.6×2 | 6.3×2 | 10×2 | 14×2 | ||||
Air pressure | kg/cm2 | 6 | 6 | 6 | 6 | ||||
Stroke | mm | 70 | 70 | 80 | 100 | ||||
Die cushion work part dimension | mm2 | 350×235×2 sets | 410×260×2 sets | 540×350×2 sets | 640×470×2 sets |
Download PDF
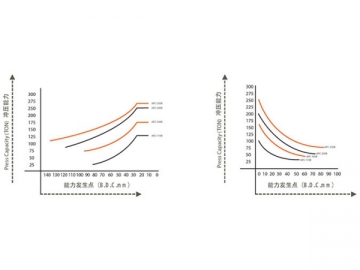