Cast Iron Worm Speed Reducer
The WP series of iron cased worm gearboxes are a newly developed product, developed using a combination of advanced technology from both at home and abroad.
· Speed reducing transmissions in various machinery (such as plastic machinery)
· Metallurgy industry
· Beverage industry
· Mining industry
· Crane transportation
· Chemical industry
· Architecture
Power and Torque | Input Power (KW) | Output Torqur(N.m) | ||||||||||||
Ratio | 10 | 15 | 20 | 25 | 30 | 40 | 50 | 10 | 15 | 20 | 25 | 30 | 40 | 50 |
Size | ||||||||||||||
40 | 0.4 | 0.33 | 0.26 | 0.24 | 0.22 | 0.16 | 0.14 | 19 | 23 | 20 | 25 | 25 | 20 | 22 |
50 | 0.65 | 0.52 | 0.4 | 0.37 | 0.34 | 0.27 | 0.24 | 31 | 36 | 32 | 38 | 39 | 36 | 37 |
60 | 1 | 0.82 | 0.65 | 0.59 | 0.54 | 0.45 | 0.4 | 50 | 58 | 56 | 68 | 62 | 71 | 75 |
70 | 1.6 | 1.35 | 1.1 | 0.96 | 0.82 | 0.67 | 0.61 | 83 | 98 | 101 | 112 | 99 | 104 | 113 |
80 | 2.2 | 1.78 | 1.36 | 1.28 | 1.2 | 0.9 | 0.8 | 113 | 133 | 120 | 149 | 151 | 140 | 145 |
100 | 3.6 | 3.1 | 2.6 | 2.35 | 2.1 | 1.68 | 1.3 | 193 | 237 | 258 | 284 | 277 | 291 | 257 |
120 | 5.2 | 4.35 | 3.5 | 3.25 | 3 | 2.2 | 1.9 | 262 | 336 | 361 | 404 | 413 | 392 | 399 |
135 | 9.75 | 7.85 | 6 | 5.5 | 5 | 3.69 | 2.89 | 540 | 622 | 619 | 696 | 707 | 667 | 626 |
147 | 10.71 | 8.43 | 6.18 | 5.71 | 5.23 | 3.84 | 3.09 | 586 | 676 | 637 | 727 | 739 | 694 | 669 |
155 | 12.8 | 9.9 | 7 | 6.53 | 6 | 4.4 | 3.61 | 709 | 785 | 722 | 842 | 848 | 784 | 770 |
175 | 17.3 | 13.6 | 10 | 9.13 | 8.3 | 6.18 | 4.85 | 958 | 1091 | 1044 | 1221 | 1189 | 1133 | 1127 |
200 | 22.6 | 18.2 | 13.86 | 12.75 | 11.67 | 8.78 | 6.71 | 1280 | 1477 | 1482 | 1643 | 1782 | 1654 | 1516 |
250 | 33.2 | 27.4 | 21.6 | 20 | 18.43 | 14 | 10.43 | 1881 | 2266 | 2310 | 2579 | 2745 | 2674 | 2357 |
Note: At present, there is no data available for models 147 WPW (A.S.X.O.T.V) and WPWK(A.S.O.T.V)
WPD.WPDK.WPWD.WPWDK.(A.S.X.O.T.V) Input Power and Output Torque Sheet: Speed of input shaft is 1500r/min (Match with Motor AO2 or Y series)Power and Torque | Input Power (KW) | Output Torqur(N.m) | ||||||||||||
Ratio | 10 | 15 | 20 | 25 | 30 | 40 | 50 | 10 | 15 | 20 | 25 | 30 | 40 | 50 |
Size | ||||||||||||||
40 | 0.12 | 6 | 8 | 9 | 13 | 14 | 15 | 19 | ||||||
50 | 0.18 | 9 | 12 | 14 | 19 | 20 | 24 | 28 | ||||||
60 | 0.37 | 19 | 26 | 34 | 42 | 42 | 58 | 67 | ||||||
70 | 0.75 | 0.37 | 39 | 54 | 70 | 87 | 95 | 58 | 68 | |||||
80 | 1.5 | 0.75 | 77 | 112 | 142 | 174 | 189 | 117 | 136 | |||||
100 | 1.5 | 80 | 115 | 149 | 181 | 198 | 260 | 307 | ||||||
120 | 3 | 2.2 | 151 | 232 | 310 | 372 | 413 | 392 | 480 | |||||
135 | 4 | 3 | 219 | 321 | 413 | 509 | 565 | 542 | 649 | |||||
147 | 4 | 3 | 219 | 321 | 413 | 509 | 565 | 542 | 649 | |||||
155 | 5.5 | 4 | 305 | 411 | 525 | 709 | 760 | 713 | 853 | |||||
175 | 7.5 | 5.5 | 415 | 602 | 783 | 1002 | 1074 | 1008 | 1278 | |||||
200 | 11 | 7.5 | 623 | 892 | 1176 | 1417 | 1680 | 1413 | 1695 | |||||
250 | 15 | 11 | 850 | 1246 | 1604 | 1933 | 2234 | 2101 | 2486 |
Note: At present, there is no data available for models 147 WPW (A.S.X.O.T.V) and WPWK(A.S.O.T.V)
WPD.WPDK.WPWD.WPWDK.(A.S.X.O.T.V) Input Power and Output Torque Sheet: Speed of input shaft is 1500r/min (Match with Motor AO2 or Y series)Size | Power and Torque | WPE.WPEK.WPEW.WPWEK | WPED.WPEDK.WPWED.WPWEDK | ||||||||||||
Ratio | Ratio | ||||||||||||||
200 | 300 | 400 | 500 | 600 | 800 | 900 | 200 | 300 | 400 | 500 | 600 | 800 | 900 | ||
40-70 | Input Power (KW) | 0.48 | 0.34 | 0.28 | 0.25 | 0.23 | 0.2 | 0.17 | 0.12 | 0.12 | 0.12 | 0.12 | 0.12 | 0.12 | 0.12 |
Output Torque (N.m) | 250 | 250 | 250 | 250 | 250 | 250 | 250 | 63 | 88 | 107 | 120 | 130 | 150 | 177 | |
50-80 | Input Power (KW) | 0.65 | 0.51 | 0.42 | 0.38 | 0.31 | 0.29 | 0.25 | 0.18 | 0.18 | 0.18 | 0.18 | 0.18 | 0.18 | 0.18 |
Output Torque (N.m) | 350 | 350 | 350 | 350 | 350 | 350 | 350 | 97 | 124 | 150 | 166 | 203 | 217 | 252 | |
60-100 | Input Power (KW) | 0.95 | 0.67 | 0.52 | 0.44 | 0.4 | 0.35 | 0.33 | 0.37 | 0.37 | 0.37 | 0.37 | 0.37 | 0.37 | 0.37 |
Output Torque (N.m) | 500 | 500 | 500 | 500 | 500 | 500 | 500 | 195 | 276 | 356 | 420 | 463 | 529 | 561 | |
70-120 | Input Power (KW) | 1.64 | 1.18 | 0.91 | 0.84 | 0.71 | 0.58 | 0.54 | 0.75 | 0.75 | 0.75 | 0.75 | 0.37 | 0.37 | 0.75 |
Output Torque (N.m) | 840 | 840 | 840 | 840 | 840 | 840 | 840 | 384 | 534 | 692 | 750 | 486 | 536 | 887 | |
80-135 | Input Power (KW) | 2.5 | 1.75 | 1.39 | 1.19 | 1.08 | 0.98 | 0.85 | 1.5 | 1.5 | 1.5 | 1.5 | 0.75 | 0.75 | 1.5 |
Output Torque (N.m) | 1400 | 1400 | 1400 | 1400 | 1400 | 1400 | 1400 | 616 | 880 | 1108 | 1294 | 1010 | 1071 | 1426 | |
80-147 | Input Power (KW) | 2.79 | 2.1 | 1.71 | 1.47 | 1.34 | 1.2 | 1.06 | 1.5 | 1.5 | 1.5 | 1.5 | 0.75 | 0.75 | 1.5 |
Output Torque (N.m) | 1575 | 1575 | 1575 | 1575 | 1575 | 1575 | 1575 | 662 | 902 | 1208 | 1316 | 1300 | 1321 | 1575 | |
100-155 | Input Power (KW) | 3.69 | 2.92 | 2.41 | 2.07 | 1.89 | 1.69 | 1.5 | 1.5 | 1.5 | 1.5 | 1.5 | 1.5 | 1.5 | 1.5 |
Output Torque (N.m) | 2100 | 2100 | 2100 | 2100 | 2100 | 2100 | 2100 | 854 | 1079 | 1307 | 1522 | 1667 | 1864 | 2100 | |
120-175 | Input Power (KW) | 5.09 | 3.91 | 3.27 | 2.72 | 2.53 | 2.5 | 2.05 | 3 | 3 | 3 | 3 | 2.2 | 2.2 | 3 |
Output Torque (N.m) | 3050 | 3050 | 3050 | 3050 | 3050 | 3050 | 3050 | 1798 | 2340 | 2798 | 3050 | 2500 | 2685 | 3050 | |
135-200 | Input Power (KW) | 7.22 | 5.41 | 4.46 | 3.83 | 3.46 | 2.91 | 2.71 | 4 | 4 | 4 | 4 | 3 | 3 | 4 |
Output Torque (N.m) | 3950 | 3950 | 3950 | 3950 | 3950 | 3950 | 3950 | 2188 | 2920 | 3543 | 3950 | 3950 | 3950 | 3950 | |
155-250 | Input Power (KW) | 11.71 | 8.14 | 6 | 5.14 | 4.67 | 4.07 | 3.67 | 5.5 | 5.5 | 5.5 | 5.5 | 4 | 4 | 5.5 |
Output Torque (N.m) | 6050 | 6050 | 6050 | 6050 | 6050 | 6050 | 6050 | 2841 | 4087 | 5546 | 6050 | 6050 | 6050 | 6050 |
Note: At present, there is no data available for models 147 WPW (A.S.X.O.T.V) and WPWK (A.S.O.T.V)
1. Stable transmission, low vibration, impact and noise, large ratio, wide commonality- the worm gearbox can be attached to various machines.
2. Impact structure: the single ratio is large and the gearbox features a better self-locking function, thus allowing the brake unit to be saved for machinery that involves a braking request
3. Higher demand for lubricating and cooling.
4. Connecting methods of input shaft: Basic type (single input shaft and double input shaft), motor flange type.
5. Combine 2 or 3 sets of gearboxes to obtain a multiple stage reducer, which leads to a greater ratio
6. The worm gearbox is suitable for omnibearing installation, and can be installed on multiple surfaces. The hollow output shaft, and various input and output types allow the gearbox to be easily added to other transmission machinery.
1. Input power (the input power capacity)
2. Ratio: speed of input shaft / speed of output shaft- When the gearbox is moved using a belt-pulley, chain wheel or couplings, the input speed should not exceed 2,000 r/min, though the most common speed range is 600 to 1800rpm. If the speed is too high, the bearing friction will be heaver, and the service life will be shortened.
3. Output torque (allowable load capacity of gearbox) = Ratio x input torque
4. Efficiency = output speed/input power x 100% - As there is friction and vibration inside the gearbox as it operates, some of the energy is transformed into a non-working consumption variety such as thermal energy. The efficiency is the utilization factor of the gearbox input energy, therefore, different models and ratios in the gearboxes lead to different levels of efficiency.
5. Turning direction of input and output shafts- The turning direction depends on the worm thread's direction. When the input shaft rotates clockwise, so will the output shaft.
6. Working condition co-efficiency: Values shown in the catalogue are for reference. The strength of the input power capacity and allowable load capacity are calculated and based on working conditions that include continuous operation for 8 hours and a stable loading process. While the actual working conditions may not match ideal conditions, please take your conditions into consideration when choosing a gearbox. Values are shown in our catalogue for your reference.
The revised output torque = theoretical output torque x working condition factor
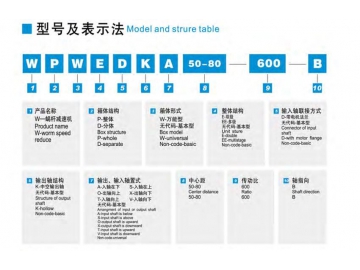
1. There is a greater friction consumption for mesh in the worm thread and worm gear surface, making the transmission efficiency lower than the gears, as well as making radiation and high temperatures more common.
2. It is easy to pair. The worm and worm gear as made based on national standards, as are the bearing and oil seal.
3. The box type is divided into basic type (with a horizontal or vertical structure footing plate) and universal type (the box is cubed with a fixed screw hole in multiple faces, and structures that have no footing plate or no footing plate addition needed)
4. Position and direction of output & input shaft: The input shaft is on the top or at the bottom, the output shaft is upward or downward, and a second input shaft upward or downward.
Before operating the worm gear reducer, please add N220 ~ N320 (ambient temperature: 30-40°C), N320 ~ N460 (ambient temperature: 40-65°C), lubricate the oil up to the center line of the oil gauge. Users should also remove the small, tapered plug from the breather. Clean the interior and inject new lubrication oil after the reducer has been used for 100 hours. After that, the oil needs to be changed after every 2500 hours of operation.