Block Production Line (Fully Automatic)
Configurations
The fully automatic block production line mainly comprises concrete batching system, block forming system, block transfer system and cuber, electrical control systems, etc.
Block Making Production Line Flow Chart
1. Cement Silo
2. Batching Machine
3. Wheel Loader
4. Screw Conveyer
5. Cement Scale
6. Pigment Mixer
7. Base Material Mixer
8. PLC Controller
9. Mixing Platform
10. Belt Conveyer for Base Material
11. Belt Conveyer for Pigment
12. Block Making Machine
13. Color Feeding System
14. Control Room
15. Green Block Conveyer
16. Elevator
17. Finger Cart
18. Lowerator
19. Lower Board Conveyer
20. Pallet Cleaning Machine
21. Pallet Turnover
22. Cuber
23. Pre-Cuber Device
24. Block Straping Machine
25. Finished Goods to Yard Conveyer
26. Pallet Return Device
27. Industry Overpass
28. Pallet Storage Davice
29. Forklift
30. Curing Room
Working Principle of the Block Making Production Line
This Block Making Production Line can realize the fully automatic production process from material batching, mixing, forming, drying and stacking, and its working principle is as follows:
1. The wheel loader feeds the course materials such as sand, gravel to the batching machine, which will be weighed by the electrical scale weighs;
2. The batched material will be fully automatic delivered to the mixer through belt conveyor, and the fine materials such as cement and fly-ash also will also be transferred to the mixer fully automatic by screw conveyor;
3. The mixed materials will be delivered to the hopper of the block making machine, and the material cart begins to charge material into the surface of the mould box, then the squeeze head drops down, it is by vibration and pressure to form blocks;
4. The green blocks on the pallets will move to the Elevator, the son finger cart leave the mother finger cart to take them and go back to the mother finger carts then moves back to the curing room, and put these green blocks together pallets on the fixed place in the curing room;
5.The finger carts also take the dried blocks with pallets to the lower board conveyor for the cuber to clip them to the wood rack on the finished goods conveyor, then we take the dried blocks from the finished goods yard with forklift, and the empty pallet on the lower board conveyor will come back to the pallet storage for the next production.
Features of the Block Making Production Line
Fully automatic production;
The blocks are dried by steaming
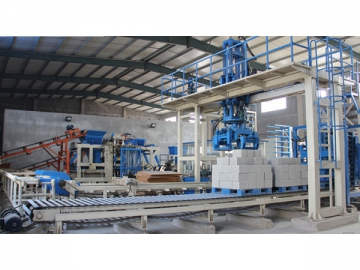
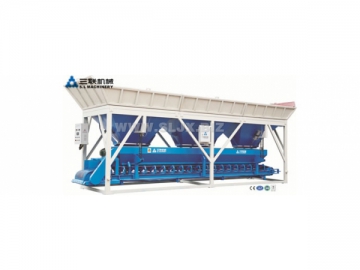
Description of the Concrete Batching System
1. The PL series concrete batching machine carries out automatic batching of sand, stone, and some other aggregates according to the concrete ratio which has been set by the user in the PLC.
2. It mainly consists of silo, weighing system, material feeding system, electrical control system, etc. And materials are feeding by pneumatic valve and belt conveyor.
3. The dosing machine is deal equipment for industrial construction project, small or medium-sized construction sites and prefabrication factories.
4. Constructed from high quality and strength steels including Q235, Q345, 45#, among others, with hardening, tempering and carburizing treatments, the concrete batching system features high longevity.
5. After every production, the concrete batcher will formulate dosing report and provide date, time, serial number and real consumption of each kind of material. It can control batching accuracy within 5%.
Specifications of PL Series Batching System
1. PL1600 Batching Machine
-- Equipped with 3 bins, the volume of each bin is 7m3
-- Productivity: 96m3/hour
2. PL1200 Batching Machine
-- Equipped with 3 bins, the volume of each bin is 4m3
-- Productivity: 72m3/hour
3. PL800 Batching Machine
-- Equipped with 2 bins, the volume of each bin is 4m3
-- Productivity: 48m3/hour
Type | Volume of Weigh Hopper (m3 ) | Volume of Unloading Hopper (m3 ) | Productivity (m3 /h) | Maximum Magnitude | Batching Category of Aggregate | Height of Loading Material (mm) | Batching & Discharging Mode | Power (kw) | Frame Dimension (mm) | Net Weight (T) |
2m ×2 | 0.8 | 48 | 1.5T | 2 | 2300 | horizontal | 6.6 | 5470×1820×2700 | 2 | |
4m ×3 | 1.2 | 72 | 2T | 3 | 2500 | 10.6 | 8531×2000×2900 | 3.5 | ||
| 7m ×3 | 1.6 | 96 | 3T | 3 | 2900 | 13 | 11650×2300×3450 | 5 | |
7m ×4 | 1.6 | 96 | 4T | 4 | 2900 | 16 | 15200×2300×3450 | 7 |
- Cement Silo
- Cement Silo
Descriptions of Concrete Mixing System
Comprising mixing system, elevating system, water supply system and electrical control system, the concrete mixer is used to mix various materials after dosing and produce needed mixture for concrete blocks.
Engineered from high quality steels including Q235, 40Cr, 45#, cast steel, etc. with hardening, tempering, carburizing, chrome plating and other treatments for some materials, the concrete mixing machine is sure to serve for a long time.
Features of Concrete Mixing System
1. Controlled by flow valve, water supply is accurate, ensuring the product humidity and reducing product strength deviation.
2. The mixing machine is a forced mixer which can mix the materials quickly and effectively, thus improving productivity.
Applications
The concrete mixing system is suitable for all kinds of prefabrication and construction projects. It is capable of mixing dry concrete, plasticity concrete, fluidity concrete, soft aggregates and all kinds of mortars.
Specifications of Concrete Mixing System
1. JS1000 Concrete Mixer
-- Productivity: 60m3/hour
2. JS750 Concrete Mixer
-- Productivity: 45m3/hour
3. JS500 Concrete Mixer
-- Productivity: 30m3/hour
4. JS350 Concrete Mixer
-- Productivity: 21m3/hour
Type | ||||
Charging Volume (L) | 560 | 800 | 1200 | 1500 |
Discharging Volume (L) | 350 | 500 | 750 | 1000 |
Productivity(m3/h) | ≥17.5 | ≥25 | ≥37.5 | ≥50 |
Max. Grain Size of Aggregate (mm) | 60 | 60 | 60 | 60 |
Speed of Mixing Blade (r/min) | 35 | 35 | 32.6 | 32.6 |
Mixing Blade (PCS) | 3 | 14 | 14 | 16 |
Model of Mixing Motor | Y112m-4 | Y180m-4 | Y200L-4 | XWDY9-17-185-6P |
Power of Mixing Motor (KW) | 5.5 | 18.5 | 30 | 18.5x2 |
Model of Winch | JS350 | JS500 | JS750 | JS1000 |
Power of Winch (KW) | 4.5 | 5.5 | 7.5 | 11 |
Height of Unloading Material (mm) | 1200 | 1500 | 1600 | 2080 |
Model of Water Pump Motor | 252B21-0.37 | 252B27-0.75 | 65JDB-30 | KQW65-100 |
Power of Water Pump Motor | 370w | 750w | 1.1KW | 1.5KW |
Frame Dimension in Working Condition (mm) | 3618×1222×3453 | 4461×3050×5225 | 4950×3636×6530 | 7922×3510×6064 |
Transporting Frame Dimension (mm) | 1721×1222×2450 | 3050×2300×2500 | 4150×3636×2500 | 4200×3110×2780 |
Net Weight (T) | 2 | 4 | 6.8 | 9 |
Description
1. This QFT10-15 block making machine is widely used to produce all sizes of hollow blocks completely according to customers' specific requirements.
2. It employs PLC controlled manufacturing technique.
3. The hollow block machine ensures ease of operation.
4. Multi languages can be set on the Man-Machine interface;
5. Its easy communication between Man and Machine realizes a kind of program management.
6. Equipped with a Digital Control Panel:
-- It is a new electrical control and fault diagnostic system;
-- The operator can monitor and control machine operations;
-- The touch screen display can set the machine to the desired operating sequence;
-- Pre-vibration times, final vibration time and the number of tamps are changed automatically;
-- If the machine stops, the screen display will show where the stoppage has occurred and also the description of the fault.
7. The block making machine is designed for optimal environmental performance and energy efficiency.
8. Various models are available for your specific requirements.
Configuration
The concrete brick making machine mainly consists of material feeding and distributing system, vibrating system, pressing system, hydraulic system and electrical control system.
Main Features
1. Excellent Concrete Distributor
Due to the higher requirements for the compressive strength of concrete products (≥10Mpa), traditional distributing method is hard to feed materials into the moulds. Our QT series block making machine is equipped with arch breaking unit in the feeder. It can effectively avoid materials caking and ensure uniform feeding. Block strength error is controlled with ±2%.
2. Unique Design for Vibration and Noise Reduction
The concrete equipment employs centralized electrical control system and uses frequency converter or proportional valve to adjust vibration frequency so as to reach the optimal vibration effect and reduce noise.
3. Combined Vibration Molding
Molding box features suspension type connection method which enables the vibration force from the vibrating press to be effectively transferred to the box, ensuring fast vibration and uniform distribution. When molding, high speed compression vibrating can immediately liquefy concrete and exhaust air, thus ensuring high density and high strength.
4. Vibration Control
Vibration system of the block making machine is controlled by frequency converter or proportional valve. This allows for low frequency feeding, high frequency molding, and directional vibrating and frequency converting. Residual vibration can be effectively removed when de-molding and braking.
5. Exceptional Versatility
The concrete block press delivers exceptional versatility. Only after changing of moulds can it produce a diversity of wall blocks and pavers to match market needs.
Type | ||
Exciting Force (KN) | 100 | |
Vibration Frequency (HZ) | 0-60 | |
Power (KW) | 57.88 | |
Molding Method | Automatic charging, vibrating and pressing | |
Control Mode | Full automatic PLC control | |
Molding Cycle (S) | 15-20 | |
Frame Dimension (mm) | 8700×2500×3020 | |
Net Weight of Host Machine (T) | 12.2 | |
Bamboo Pallet | 1220×900×25 | |
Annual Output based on double shift of 300 days | block (m3) | 140,000 |
paving stone (m2) | 691,000 |
1) Bamboo pallet or wooden pallet
- Bamboo pallet
- Wooden pallet
Used to carry the block out of the main machine by conveyor. Customers can also choose the PVC pallet or steel pallet.
Note: Bamboo pallet cannot be used for the steam curing system.
2) Wheel loader
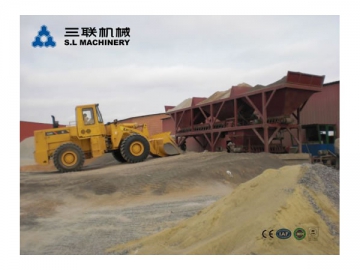
The finger car will transport the finish block into curing system, which can shorten the curing time and increase the productivity.
We welcome you to contract us to get further detailed information!
The block transfer system consists of elevator and lowerator, finger car, transport device and cuber. It can meet the layout requirements in different sites.
Working Process
Wet blocks just formed in the block making machine are elevated in certain layers and transported to the curing room in finger carts. As cured, the blocks will be transported to the cubing system and cubed based on a certain specification, and then transported to the site for further curing.
Details of the Block Transfer System and Cuber
1. Finger Cart
Fully automatic finger cart in the concrete block transport system comes with auto centering and positioning unit, auto take-up unit and real-time monitoring system which ensure the highest safety in production.
2. Cuber
Cuber in our block production line features linear track control that ensures high stability in operation. Elevating and lowering are controlled by coder and proportional valve, realizing quick, slow elevating and lowering functions and ensuring more precise cubing height. Rotation angle, cubing layers and cubing height can be adjusted.
3. Pellet Return Device
Manufactured using our proprietary technology, the pellet return device in the concrete block transfer system can is sure to return the pallets to the pellet warehouse accurately and stably.
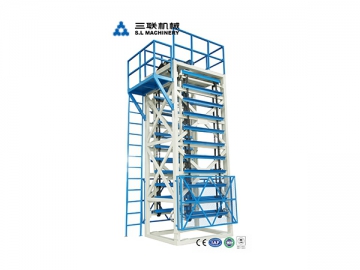
Lifting/Descent Speed | 0.1m /s |
Rotating Speed | 9.768r/min |
Distance Between Layers | 406.4mm |
Effective Transport Layers | 10layers |
Power | 7.5KW |
Frame Dimension | 2030×2120×6012mm |
Net Weight | 4T |
Maximum Load | 8T |
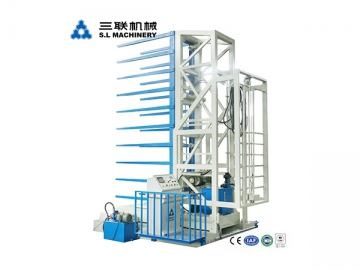
Fingers Cart Maximum Running Speed | 0.85m /s |
Distance Between Layers | 406.4mm |
Effective Transport Layers | 10 layers |
Working Pressure of Hydraulic System | 16Mpa |
Rated Flow | 25L /min |
Power | 16.45KW |
Frame Dimension | 3595×2000×4513mm |
Net Weight | 6T |
Maximum Load | 8T |
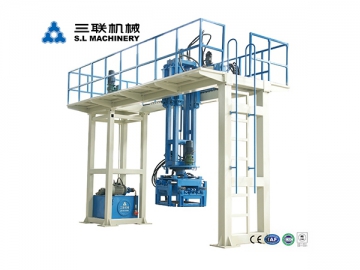
Traveling Motor | Cycloidal Reducer XWD-2.2-4-23 (electromagnetic vibration) with adjustable rotating speed |
Synchronous Belt | XH (P=22.225) |
Length | 11000mm |
Rotating Motor | XWD1.5-8135-43with adjustable rotating speed |
Rotating/Reversing Angle | ±90° |
Working Pressure | 10MPa |
Maximum Hoisting Weight | 650Kg |
Oil Pump Power | 18KW |
Rated Flow | 70L /min |
Effective Clamping Height | 1200mm |
Major Clamping Range | 820mm -1220mm [Q(F)T10-15] 760mm -1160mm [Q(F)T12(XL)-15] |
Minor Clamping Range | 650mm -900mm [Q(F)T10-15] 760mm -1160mm [Q(F)T12(XL)-15] |
Cycle Period | 30s (adjustable) |
Thickness of Clamped Product | (max) 300mm, (min) 50mm |
Frame Dimension | 6350×2760×5992mm |
Net Weight | 8T |
The equipment shown below is optional for our concrete block production line. They are specially designed to maximize the productivity of our whole block making system.
Bamboo pallets or wooden pallets are used to carry formed blocks out of the block machine by conveyor. PVC Pallets and Steel pallets are steel available.
Note: Bamboo pallet can not be used for steam curing system.
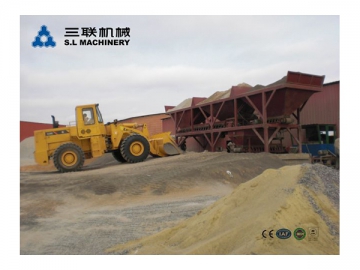
Wheel loader is used to carry raw materials from storage yard to the batching system. It boasts large handling capacity and improves production efficiency.
Finger cars will transport the finish blocks into the curing system, shortening curing time and increasing the productivity.
Main Features
1. Via high performance digital logic control system, the concrete block plant can carry out centralized monitoring to field working conditions and conduct data recording, parameter setting, regular file saving, report printing, and other operations.
2. It is able to monitor the equipment running status, real-time data and previous data and process, save and print the data.
3. By collection and processing of the real time data, the block production line enables you to directly know its whole production conditions and thereby dramatically improve productivity, enhance efficiency and realize high automation.
4. The automatic block making machinery employs Siemens electrical components to improve service life and operational stability.
Applications
The block production line is fully automatic and stationary concrete and coal ash processing equipment. By changing moulds, it can be used to make a vast variety of blocks for varied applications.
1) Concrete wall blocks: hollow blocks, solid brocks, blocks with multi rows of holes, insulating blocks, etc.
2) All kinds of paving blocks: Interlock blocks, Dutch bricks, curbstones and various special concrete members and blocks for park, airport and port constructions.
The block production line is excellent for making high quality, high strength concrete blocks or coal ash blocks. It comes in various configurations to match customers' needs.