PA (nylon) precision tube extrusion line
PA (nylon) Pipe Extrusion Line / PA Precision Tube Extrusion Line / Nylon Tube Extrusion Line
Due to its excellent resistance against bending, fatigue, stretching, chemical corrosion, gas, sel oil, lubricating oil, and its smooth inner wall, the PA (nylon) pipe has been widely used in automobile fuel oil systems, braking systems, special material conveyance and other areas, bringing an additional high product value and excellent market prospect to customers all over the world. Existing materials for the automobile pipeline include PA11, PA12, PA6, PA66, and PA612.
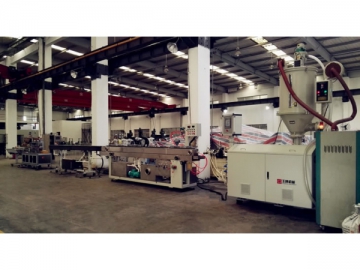
Based on past manufacturing experience and the use of Japanese technology, we have developed the 3rd generation PA precision tube extrusion line, which has become increasingly popular among customers both at home and abroad. Our end users include CHINAUST Group, Sanoh Industrial, Arkema and HUATE Group.
Case show:
End-user: HUATE Group
Project start date: 2015
Machine line: PA11/12 Oil tube EXTRUSION LINE
Machine line quantity: 1 line
Capacity: 60-80KG/h
Equipment Features
The PA (nylon) screw is a DSVM-T MADDOCK Barrier type mixing conveying screw that easily adapts to the use of PA material with a high thermal sensitivity, flow rate and melting viscosity, thus ensuring an even plasticization and high output efficiency.
The core rods and die are made of Swedish ASSAB S136 die steel, and the precision grinding ensures the inner flow surface glossiness and corrosion resistance. The mold structure uses a high pressure volumetric type which was developed by our company, and provides a stable, high speed extrusion for the tube material with very little fluctuations.
With a new automatic and accurate control of the vacuum technology, the vacuum and water system are separately controlled. By doing so, we can coordinate the multilevel water balance control system with the vacuum system and ensure a stable vacuum performance, cooling water level and water flow.
The high performance LaserMike measuring system forms a closed loop feedback control, which eliminates diameter deviation online.
The puller is equipped with a multi-layer wear resistance synchronous belt, with no sliding. The high precision roller drive traction, YASKAWA servo driving system, or the ABB AC driving system all achieve a stable pulling performance.
Based on the servo drive system, Japan’s Mitsubishi PLC programmable control, and SIEMENS human to computer interface, the cutter achieves precision continuous cutting, timing cutting, length counting cutting and more. The cutting length can be freely adjusted, and the cutting times set automatically in order to meet different cutting requirements for the cutting length.
-
Die
-
Calibration sleeve
-
Vacuum cooling tank
-
Laser gauge
-
Puller and cutter
-
Collection tank
Model | Process pipe diameter range (mm) | Screw diameter (mm) | L/D | Main power (KW) | Output (Kg/h) |
SXG-45 | 3.0 ~ 12.0 | 45 | 30 | 15 | 18-30 |
SXG-50 | 3.0 ~ 16.0 | 50 | 30 | 18.5/22 | 28-45 |
SXG-65 | 3.0 ~ 20.0 | 65 | 30 | 37/45 | 55-85 |
SXG-75 | 3.0 ~ 20.0 | 75 | 30 | 55/75 | 80-110 |
OD(mm) | Producing speed (m/min) | Diameter control accuracy (≤mm) |
4.0 | 80-100 | ±0.05 |
6.0 | 60-80 | ±0.05 |
8.0 | 40-50 | ±0.08 |
10.0 | 25-40 | ±0.08 |
12.0 | 16-30 | ±0.10 |
14.0 | 12-20 | ±0.10 |
16.0 | 10-15 | ±0.12 |
Cutting length | ≤50mm | ≤500mm | ≤1000mm | ≤2000mm |
Cutting accuracy | ±0.5mm | ±1.0mm | ±2.0mm | ±3.0mm |