Pressure Screen (Inward Flow)
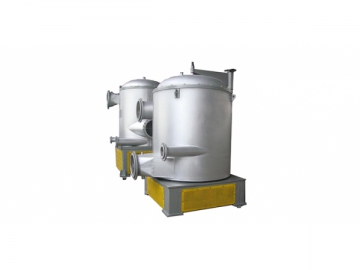
Capacity: 20-250 t/d
This pressure screener is designed with an inward flow structure and is used for the fine screening of pulp for pulping systems and screening of pulp prior to entering the paper machines. This screening equipment consists of the screen body, rotor, cylinder, driving part and lifting device.
Main Features of the Pressure Screen
1. High Screening Efficiency
As the pulp enters the screen along a tangential direction under high pressure, fibers and coarse impurities are screened before the pulp enters the cylinder under centrifugal force. Accepted fiber will quickly pass through the screen cylinder depending on pressure differences between the inlet and outlet.
2. Long Service Life
Heavy impurities are filtered by using centrifugal force after the pulp enters the pressure screen, in order to reduce impact and wear to the rotor wing, and cylinder. It is also designed to extend the service life of the cylinder.
3. No Clogging
These pulps are screened in a uniform manner from top to bottom, without thickening and clogging, as the impurities are moved away from the screen cylinder.
4. It can replace the low frequency screen
Accepted pulp from the pressure screen come with a low pulse strength and can be directly delivered to the forming table without generating a disturbance.
5. High Quality Pulp
The screen cylinder is manufactured from stainless steel with a thin screen cut, significantly improving the removal rate of the impurities in the accepted pulp.
6. Low Maintenance Cost
The main shaft of the pressure screen comes with an advanced mechanical sealing system, making it more difficult to damage.
Model | ||||
Screening area (m2) | 0.6 | 1.2 | 2 | 3 |
Screen cut width (mm) | 0.15-0.55 | |||
Inlet pressure (Mpa) | 0.1-0.25 | |||
Outlet pressure (Mpa) | 0.01-0.04 | |||
Screening consistency (%) | 1.0-2.0 | |||
Capacity (t/d) | 20-60 | 25-90 | 40-150 | 50-250 |
Motor power (kW) | 15-18.5 | 22-30 | 37-45 | 55-75 |
Working Principle
The pulp enters the cavity between the screen body and the cylinder. By relying on the pressure differences between two sides of the cylinder, the accepted fibers will flow into the cylinder through holes, and be discharged from the lower outlet. The rejects left outside the cylinder will be removed from the screen through the discharge hole under the pulp pressure and pushed using a rotor. In addition, high speed rotation of the rotor can clean the cylinder.
Maintenance
1. The bearing needs to be kept lubricated, and must be greased once a week.
2. Regularly inspect the axis and ensure the temperature rise does not exceed 35º.
3. Do not screen metal and other large impurities.
4. The rubber oil seal should change once every six months to guarantee a high sealing performance.