Vertical Roller Mills
With many years of experience in technical innovation within the field of cement and slag grinding, CITIC Heavy Industries (CITIC HIC) has successfully developed various models of vertical roller mills. Our team of experts will help global customers develop a reliable, energy-saving and high-efficiency vertical roller mill grinding solution by taking advantage of our technological development strength, core manufacturing expertise, strict quality control measures and excellent customer service.
At our powerful national key laboratory, CITIC HIC has established a vertical roller mill testing platform to conduct trials and tests of different materials, thus identifying the best solution of vertical roller mill selection.
Our engineers employ FEA software to analysis, calculate and optimize the structural strength of grinding roller shaft, rocker arm, grinding table and other key components, ensuring the high reliability of machine operation.
- Fluid flow
-
A professional fluid flow simulation software is adopted to analyse fluid flows and optimize the internal structure of vertical roller mill.
- Transmission
-
The large vertical planetary gear reducer was developed using state-of-the-art technology. With a construction of one bevel gear stage and two planetary gear stages, the gear unit features high transmission accuracy, uniform stress distribution and high load bearing capacity. The gearbox service factor is greater than 2.5 in accordance with AGMA standard.
- Classifier / separator
-
The dynamic classifier is integrated in the VRM mill, providing high accuracy, high efficiency, low pressure drop and low energy consumption.
- Control
-
The advanced control system performs real-time monitoring of operating parameters. A touch screen display is configured for easy control, enabling the machine to be operated highly automatically, continuously and stably.
- Full-process solution
-
Equipment design → Project design → Equipment configuration → Installation & commissioning through to turnkey project acceptance sign off
Model | Capacity | Matching clinker line output | Grinding table diameter | Main reducer | Main motor power |
t/h | t/d | mm | kW | ||
LGM7027 | 820-880 | 10000 | 7000 | MZL710 | 7200-7600 |
LGM6027 | 600-650 | 7000 | 6000 | MZL600 | 5500-6000 |
LGM5426 | 500-550 | 6000 | 5400 | MZL480 | 4600-5000 |
LGM5024 | 400-450 | 5000 | 5000 | MZL370 | 3800-4200 |
LGM4521 | 300-350 | 3500 | 4500 | MZL300 | 3150-3300 |
LGM4018 | 200-250 | 2500 | 4000 | MZL200 | 2000-2200 |
LGM3216 | 120-150 | 1500 | 3200 | MZL170 | 1200-1500 |
Model | Capacity | Annual output | Grinding table diameter | Main reducer | Main motor power |
t/h | t/a | mm | kW | ||
LGMS7027 | 280-300 | 2,000,000 | 7000 | MZL800 | 8000 |
LGMS6027 | 210-230 | 1,500,000 | 6000 | MZL600 | 6300 |
LGMS5525 | 165-180 | 1,200,000 | 5500 | MZL480 | 5000 |
LGMS5527 | 125-135 | 1,000,000 | 5500 | MZL370 | 4200 |
LGMS4624 | 90-95 | 600,000 | 4600 | MZL300 | 3000 |
LGMS4018 | 60-65 | 450,000 | 4000 | MZL200 | 2200 |
LGMS3218 | 45-50 | 300,000 | 3200 | MZL170 | 1800 |
Model | Capacity | Grinding table diameter | Main reducer | Main motor power |
t/h | mm | kW | ||
LGMC7027 | 320-350 | 7000 | MZL710 | 7200-7600 |
LGMS6027 | 210-230 | 6000 | MZL600 | 5800-6300 |
LGMC5725 | 220-240 | 5700 | MZL480 | 4800-5000 |
LGMC5527 | 160-180 | 5500 | MZL370 | 4000-4200 |
LGMC4624 | 120-140 | 4600 | MZL300 | 2800-3000 |
LGMC4018 | 70-80 | 4000 | MZL200 | 2000-2200 |
LGMC3218 | 55-60 | 3200 | MZL170 | 1600-1800 |
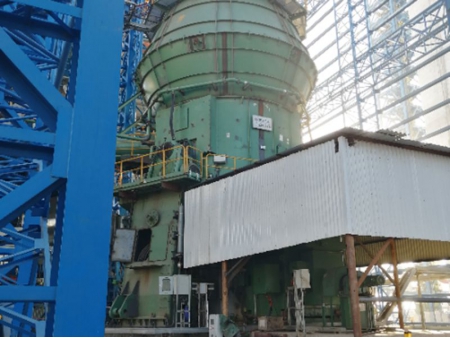
Liugang Group's Fangchenggang Iron and Steel Base
2 vertical roller mills for slag (LGMS5727), annual output 1,400,000 ton
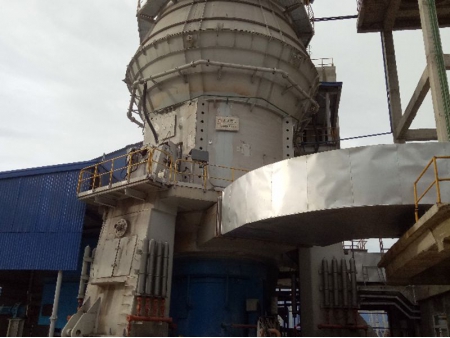
Vietnam Hoa Phat Group
Vertical roller mill for high specific surface area of 520m2/kg, annual output 900,000 ton
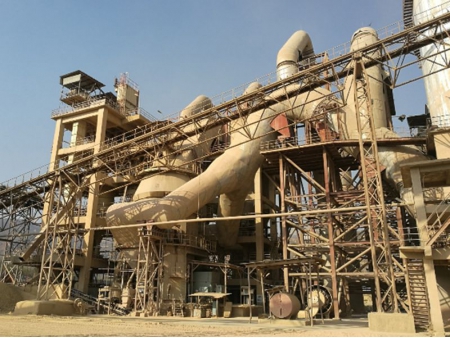
Pakistan GCL International
Vertical roller mill for cement (LGMC5725, 225t/h), annual output 1,600,000 ton
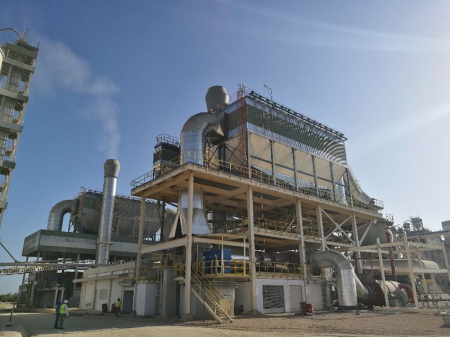
Dominica Cement Project
2 vertical roller mills for cement (LGMC4018), annual output 500,000 ton
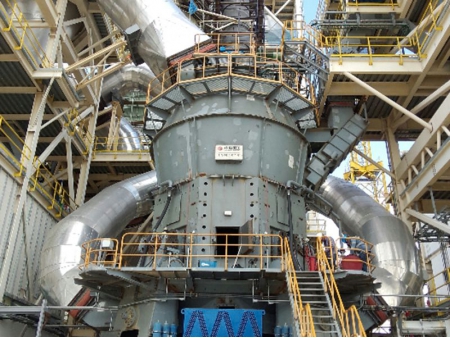
Dominica Clinker Project
Vertical roller mill for raw material (LGM4018, 2500t/d)
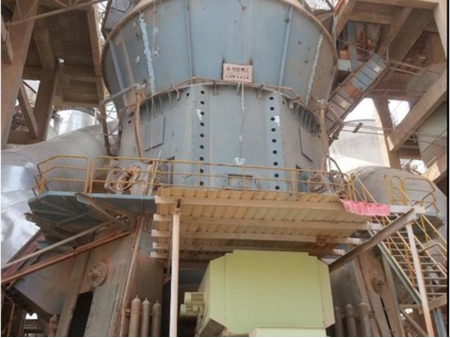
Anhui Fengyang Zhongdu Clinker Project
Vertical roller mill for raw material (LGM5426, 6000t/d)
- Forward thinking design
Cutting-edge design concept, adoption of international standards
30 years of experience in developing and nurturing innovative technology of vertical roller mill - High reliability
High-grade materials, top-notch process, advanced technologies synchronised with international level bring longer service life of equipment - Low operaion cost
Rational selection of equipment for reduced energy consumption, reliable hydraulic and electrical control technologies result in green eco-friendly operation and improved energy efficiency - Excellent service
Operation and maintenance training, on-site installation guide, commissioning and trial running (mechanical, hydraulic and electrical systems), high quality original spare parts supply
- Manufacturing
Casting and Forging Capacity
We have four production lines that have the capacity to produce large steel castings, large high-value forgings, large annular parts and large non-ferrous metal parts respectively. - Service
Lifetime service
With state-of-the-art technology and rich experience, CITIC HIC works through each critical step to individualize the optimal process and performance as per customer needs. Our lifetime service covers equipment installation, testing, maintenance, refurbishing, remote monitoring & diagnosis, upgrading & retrofitting, and performance guarantee.