Anti Corrosion APVC Roofing Sheet
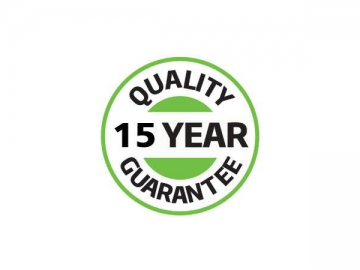
1. Long Term Color Stability and Long Lifespan
2. Excellent Anti-Corrosion & Anti-UV Performance
The anti corrosion APVC roofing sheet is developed based on international advanced technologies. It is an especially designed roofing material for corrosive substance manufacturing factories and areas with frequent acid rain.
Similar to our other types of construction material, this type is also produced based on multi-layer co-extrusion technology through one-time processing. Two-, three-, or four-layer co-extruded ASA-PVC sheeting materials are all available. Each layer of material offers the product a distinct feature. The typical layers of material for our anti corrosion APVC roofing sheet are listed below.
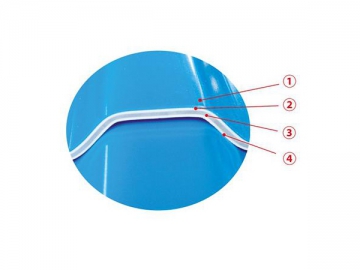
- It is a kind of resin with superior weather resistance. Due to its resistance to UV radiation and chemical corrosion, this material provides our APVC roofing sheet with great durability
- Good quality modified PVC materials with high toughness is adopted to ensure the strength while without compromising on the rigidity.
- The special foam structured material which delivers good heat and sound insulation.
- Adopts a kind of white color high toughness material, which gives the building a sense of and increases internal brightness.
With great durability, our range of anti corrosion APVC roofing sheet is regularly used in the roofing system construction projects for sheds, warehouses, prefab houses , farmers market, high grade manufacturing plants, and so on.
Especially, it is suitable for steel mills, ceramic plants, soy sauce factories, printing and dyeing plants, organic solvent factories, as well as manufacturing plants for acid, alkali and other corrosive substances.
Steel Plant (Indonesia)
Coal Factory
Top layer: white, blue, green, beige (light yellow), grey, or customized.
Bottom layer: white or customized
White
(ART-C-001)Blue
(ART-C-002)Green
(ART-C-003)Beige (light yellow)
(ART-C-004)Grey
(ART-C-006)
Model | HB-ART | ||||||
Profile | ![]() | ||||||
Thickness | 2.0mm | 2.5mm | 3.0mm | ||||
Purlin Span | 700mm | 800mm | 900mm | ||||
Length | 5800mm, 11800mm or Customizable | ||||||
Overall Width | 1130mm | ||||||
Effective Width | 1050mm | ||||||
Slope | > 20° | ||||||
Weight | 2.0mm: 3.50 kg/m2 | 2.5mm: 4.50 kg/m2 | 3.0mm: 5.50 kg/m2 | ||||
Container Load Capacity | Thickness | SQ.M./20 FCL (21 Tons) | SQ.M./20 FCL (26 Tons) | ||||
2.0mm | 6000 m2 | 7300 m2 | |||||
2.5mm | 4600 m2 | 5600 m2 | |||||
3.0mm | 3800 m2 | 4600 m2 |
Profile Type | Model No. | Profile Drawing |
Trapezoidal (reinforced type ) | HB-P-T-1070-250-37 ( recommended ) | ![]() |
HB-P-T-1120-173-33 ( recommended ) | ![]() | |
Trapezoidal | HB-P-T-840-210-26 | ![]() |
HB-P-T-1130-210-26 | ![]() | |
HB-P-T-1350-210-26 ( recommended ) | ![]() | |
Trapezium (utilized as wall panel) | HB-P-T-1110-76-8 | |
HB-P-T-1410-76-8 | ||
Round Wave | HB-P-T-930-63-16 | |
HB-P-T-1130-63-16 |
No. | Test item | Test method | Test condition | Test result | |
1 | Tensile strength | ASTM D638-10 | Testing speed: 50mm/min | 30 Mpa | |
2 | Flexural strength | ASTM D790-10 Procedure A | Testing speed: 1.3mm/min Span: 48mm | 56 Mpa | |
3 | Temperature different between outdoor and indoor | 8℃ | |||
4 | Impact resistance | ASTM D5420-10 | Geometry: GE(Ø12.70mm) Impact weight: 0.9kg | Mean failure energy: 4J | |
5 | High temperature resistance | 60°C , 6h | No visible change | ||
6 | Low temperature resistance | -35°C , 6h | No visible change | ||
7 | Chemical resistance | 70% Ethanol solution,(V/V), Immersion test, 23°C, 2h | No visible change | ||
8 | 10% NaOH Solution,(m/m), Immersion test, 23°C, 2h | No visible change | |||
9 | Saturation NaCL Solution, Immersion test, 23°C, 2h | No visible change | |||
10 | Thermal conductivity | ASTM C518-10 | Mean temperature (°C ) | Temperature difference (°C ) | Thermal conductivity [W/(m.K )] |
25.48 | 9.36 | 0.071 | |||
11 | 20mm Vertical burning test | UL 94-2013 Section 8 | Specimen: 129x12.5x3.0mm | V-0 | |
12 | Sound | Compare with metal roof tile | 30 dB lower |
Note: The above testing results are achieved based on 3mm thick and tests conducted by SGS and are provided for reference only.
Corrosion resistant
This series of APVC roofing sheet is especially suitable for coastal areas as well as areas with frequent acid rain, due to its superior corrosion resistance. Tests have proven that the product offers no visible changes even when it is immersed in corrosive solutions (such as saline solution, alkali solution, and acid solution with concentration below 70%) for continuously 24 hours. This type of building material will never rust, thus effectively improves waterproof property.
Waterproof
Our anti corrosion APVC roofing sheets are available with unique external designs. This, coupled with our patent waterproof accessories, makes sure all the installation fittings including screws will never rust. Thus, great waterproof performance is ensured.
- Special Waterproof Fittings
- Application Project
Heat insulating
Due to great heat insulation property, the ASA-PVC roof panel has thermal conductivity coefficient of 0.07W/(m.K). The coefficient is only 1/6 that of cement tiles, and 1/2200 that of 0.5mm thick color steel tiles.
Fire resistant
Through tests conducted by SGS according to UL 94-2013 standard, this product is proven to be a non-flammable material with minimum flame rating up to V0.
Convenient and efficient installation
With maximum effective width up to 1260mm, our anti corrosion APVC roofing sheet offers higher installation efficiency than clay tiles. This reduces both material and installation cost. Meanwhile, its light weight and complete range of accessories make it easy for installation.
1. Barge Board
2. Tranparent Roofing Sheet
3. Ridge Unit
4. Roofing Sheet
5. Celling
6. Sidewall Flashing
7. Wall Cladding
These special waterproof installation accessories are independently designed by us for proper installation and fixation of our UPVC Hollow Sheet. They play important roles in fixing the sheeting materials properly. Thus avoiding water leakage and distortion as well as other unusual circumstances.We recommend using 5 sets of fittings for every square meter of roofing sheet during installation. So as to prevent water leakage and extend the service life of the roofing material.