High Pressure Steam Boiler
Rated steam output: 6-100t/h
Rated working pressure: 1.25-9.82Mpa
Fuel type: natural gas, heavy oil, light oil, city gas and methane.
The boiler uses gas and oil as fuel, and changes steam into water in order to heat water through the use of a heat exchanger. It provides heat for steam powered manufacturing equipment or general heating.
The steam boiler is used in a variety of industries, with the main applications listed below:
- Food industry: The steam can be used for cleaning, as well as heating, drying or disinfecting food.
- Spinning, printing and dying industry: used for dying, rinsing and shaping of cloth.
- Biological medicine industry: used for heating reaction kettles, condensation reaction, exchanging heat and disinfecting of chemical reaction systems.
- Hospital: used for disinfecting, heating, and air conditioning.
- Petrochemical Industry: used for heating oil and increasing liquidity.
- Wood furniture industry: used for drying wood, brick and other materials.
- Papermaking industry: High pressure steam is used to drive power generation. After decompressing, the steam is used for drying, and the last of the low-pressure steam is used for ink removal, pulping or paper production.
- Tobacco industry: provide heat for making pipe tobacco and baking.
All products of this type are sent out completely to ensure that the boiler can be installed quickly on site. With the exception of accessories for water supply, gas supply and electrical connection, the customer will receive all parts for the boiler at once, so there is no need for later construction or special installation processes. Extensive testing and debugging is carried out before the boiler leaves the factory, in order to ensure the final quality.
Type | Rated steam output (t/h) | Rated working pressure (Mpa) | Water outlet temperature (℃) | Water inlet temperature(℃) | Water volume (m3) | Design thermal efficiency(%) | Dimension(L×W×H) | |
6 | 1.25 | 193 | 104 | 13 | 92 | 5160×2700×3600 | ||
10 | 1.25 | 193 | 104 | 17 | 92 | 8460×2700×3600 | ||
20 | 1.25 | 193 | 104 | 20 | 92 | 9730×3290×3900 | ||
20 | 1.25 | 350 | 104 | 20 | 94 | 10200×3290×3900 | ||
25 | 3.82 | 400 | 104 | 22 | 94 | 11350×4080×4180 | ||
35 | 1.25 | 350 | 104 | 24 | 94 | 10350×4180×4200 | ||
40 | 1.25 | 350 | 104 | 26 | 94 | 11770×4310×4200 |
The boiler shell is made using submerged arc welding, with all longitudinal and circumferential welding undergoing 100% radiographic testing to ensure the welding effect. An automatic argon welding process is used in the pipe and plate.
Aluminum silicate fiber and refractory mortar.
The boiler temperature is controlled under 50℃.
The boiler consists of a heated surface, burner, convection pipe bundle of flue gas, heat recovery equipment, pump, instruments, valves and water treatment system.
1. Heated surface
The heated surface consists of a furnace, shell, tube sheet, long smoke tube and short smoke tube.
Features: It uses a wet-back structure, and avoids a back tube sheet that easily burns out, as it can withstand a high temperature gas flow in order to ensure the safety and reliability.
2. Combustion chamber
The combustion chamber uses a corrugated furnace to effectively reduce the thermal stress of boiler, which can improve the reliability and service life of boiler.
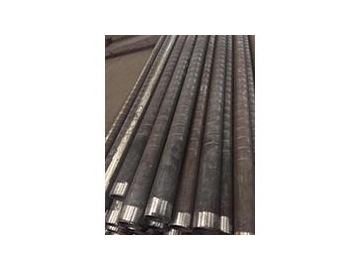
3. Convection tube bundle of flue gas
The bundle uses a spiral pipe with a high heat transfer coefficient in order to strength the heat transfer through convection, thus improving the boiler’s overall thermal efficiency.
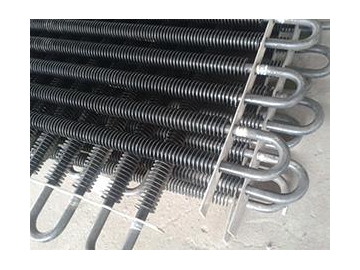
4. Back heat recovery device
This device uses a spiral finned tube and it can absorb waste heat from flue gas to save energy.