Decanter Centrifuge
Scientifically designed and meticulously crafted, the LW decanter centrifuge is a horizontal filter centrifuge that allows continuous operation and discharges solids via a screw conveyor. It is mainly used for solid-liquid separation, liquid clarification and sludge dewatering in a number of industrial process, and it fits for polyoxyethylene, sulfurous acid, strontium sulfate and more.
Main Characteristics of Decanter Centrifuge
1. Our product has a high production capacity, and its compact structure greatly facilitates operation and maintenance.
2. This separation equipment exhibits excellent serviceability when dealing with different suspensions, and it is commonly used in food, chemical, petrochemical, pharmaceutical, environment protection and other industries where solid-liquid separation is needed.
3. Our horizontal centrifuge is suitable for various materials, and it is able to deliver normal performance even if the grain size is not uniform. In addition, the solid particle size may vary from 0.005mm to 2mm.
Model | | | | | | | | | | | |
Basket diameter (mm) | 200 | 220 | 250 | 300 | 350 | 380 | 450 | 520 | 630 | 720 | 1000 |
Basket length (mm) | 600 | 930 | 1000 | 907 | 1460 | 1158 | 1800 | 2130 | 2200 | 2665 | 3000 |
Max. speed (r/min) | 5800 | 4800 | 4000 | 3800 | 4000 | 2750 | 3000 | 3200 | 2500 | 2000 | 1500 |
Max. separating factor | 3760 | 2833 | 2240 | 2420 | 3130 | 1606 | 2263 | 2976 | 2205 | 1609 | 1258 |
Processing capability (m3/h) | 0.5-1 | 0.5-2 | 0.5-3 | 2-8 | 3-12 | 3-15 | 6-20 | 12-30 | 25-35 | 45-100 | 50-110 |
Main motor power (kW) | 7.5 | 11 | 11 | 15 | 22 | 18.5 | 30 | 75 | 75 | 75 | 132 |
Dimensions (mm) | 1512 ×1200 ×688 | 1786 ×1068 ×688 | 2740 ×700 ×900 | 2168 ×1445 ×730 | 3950 ×830 ×1170 | 2600 ×1500 ×780 | 3100 ×1800 ×1200 | 4940 ×1050 ×1470 | 5120 ×1450 ×1750 | 5365 ×3200 ×1500 | 5200 ×2400 ×1950 |
Weight (kg) | 900 | 1000 | 1200 | 1300 | 2250 | 2500 | 3200 | 5600 | 7800 | 11500 | 14500 |
Material Options
According to the suspension to be processed, our decanter centrifuge’s mechanical parts that will contact liquid during work can be constructed from austenitic stainless steel (321, 316L, etc.), Hastelloy, titanium alloy or other corrosion resistant materials.
Structural Options
1. Lubrication Method: Grease lubrication or forced circulating lubrication
2. Helical Blade Number: One, two or more
3. Helical Blade Surface: Coated with high hardness alloy
Optional Configuration
1. Frequency converter and PLC controller
2. Monitoring system for vibration and temperature rise of main bearing
3. Feeding speed controller
4. Gas-liquid separation device on liquid outlet
5. Other requirements
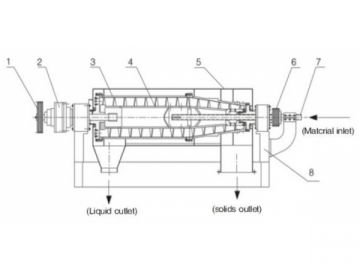
1. Belt Pulley 2. Differential Mechanism 3. Basket | 4. Screw Conveyor 5. Housing 6. Belt Pulley | 7. Feed Pipe 8. Base |